need of industry 4.0
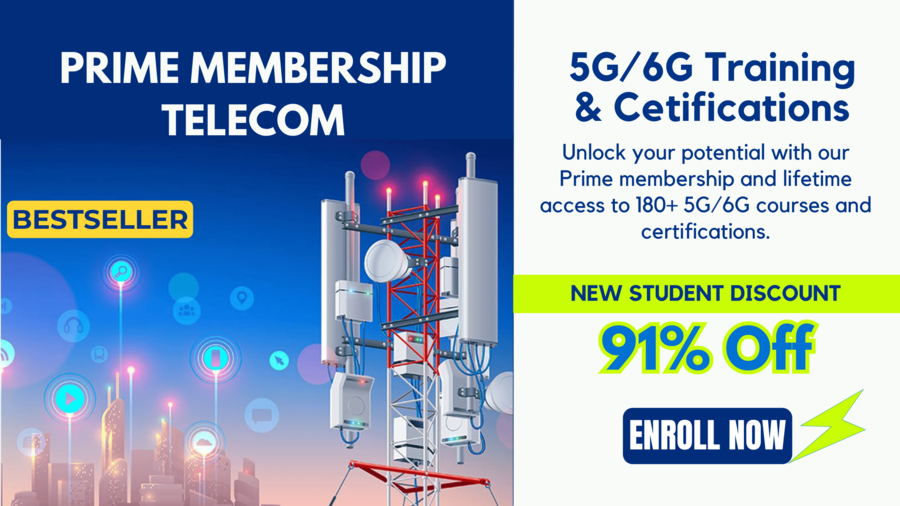
Industry 4.0, often referred to as the fourth industrial revolution, represents a paradigm shift in manufacturing and industry, driven by the integration of digital technologies, data exchange, and automation. The need for Industry 4.0 arises from various challenges and opportunities that modern industries face. Let's explore the technical details of why Industry 4.0 is considered crucial:
1. Interconnected Systems:
- Integration of Information Technology (IT) and Operational Technology (OT):
- Industry 4.0 aims to break down the traditional silos between IT and OT by creating a seamless, interconnected ecosystem where machines, devices, and systems can communicate and share data in real-time.
- Smart Factories:
- The goal is to create smart factories where all components, from machines to sensors, are connected to a central network. This connectivity enables better visibility, control, and optimization of the entire production process.
2. Data-driven Decision Making:
- Big Data Analytics:
- Industry 4.0 leverages big data analytics to process and analyze vast amounts of data generated by sensors and devices on the factory floor. This data-driven approach allows for better decision-making, predictive maintenance, and improved overall efficiency.
- Real-time Monitoring:
- Real-time monitoring of machines and processes provides insights into performance, quality, and potential issues. This enables proactive decision-making and reduces downtime.
3. Automation and Robotics:
- Autonomous Systems:
- Industry 4.0 emphasizes the use of autonomous systems and robots that can operate collaboratively with human workers. Advanced robotics and automation technologies enhance precision, speed, and efficiency in manufacturing processes.
- Flexible Manufacturing:
- Automation enables flexible and adaptive manufacturing processes, allowing quick reconfiguration of production lines to accommodate changes in product design or demand.
4. Internet of Things (IoT):
- Connected Devices:
- The IoT plays a pivotal role in Industry 4.0, with a multitude of sensors and devices connected to the internet, sharing data and interacting with each other. This connectivity enhances the visibility and control of various elements in the production environment.
- Smart Sensors:
- Smart sensors embedded in machines and products collect data on temperature, pressure, vibration, and other parameters. This data is then used for monitoring and optimizing processes.
5. Cyber-Physical Systems (CPS):
- Integration of Physical and Digital Worlds:
- CPS in Industry 4.0 involves the integration of physical components with digital systems, creating cyber-physical systems. These systems enable real-time monitoring, control, and coordination between physical processes and digital representations.
- Digital Twins:
- Digital twins, virtual representations of physical objects or systems, enable simulation, analysis, and optimization of processes and products.
6. Enhanced Efficiency and Productivity:
- Lean Manufacturing:
- Industry 4.0 promotes lean manufacturing principles by optimizing resource utilization, reducing waste, and improving efficiency. This is achieved through data-driven insights and automation.
- Predictive Maintenance:
- The ability to predict equipment failures and schedule maintenance activities based on real-time data helps prevent unplanned downtime, reducing costs and improving overall productivity.
7. Cybersecurity and Standards:
- Security Challenges:
- The increased connectivity and data exchange in Industry 4.0 introduce cybersecurity challenges. Ensuring the security of data, communication channels, and connected devices is a critical aspect.
- Standardization Efforts:
- Industry 4.0 initiatives often involve standardization efforts to establish common frameworks and protocols that ensure interoperability and security across various systems and devices.
8. Customer-Centric Production:
- Mass Customization:
- Industry 4.0 facilitates mass customization, allowing manufacturers to respond quickly to customer demands by adapting production processes and configurations.
- Agile Manufacturing:
- Agile manufacturing, enabled by Industry 4.0 technologies, allows companies to be more responsive to market changes and customer preferences.
9. Sustainable Practices:
- Resource Optimization:
- By leveraging real-time data and analytics, Industry 4.0 helps in optimizing resource usage, reducing waste, and promoting sustainable manufacturing practices.
- Energy Efficiency:
- Smart technologies contribute to energy-efficient operations, minimizing environmental impact and aligning with sustainability goals.
In summary, Industry 4.0 addresses the evolving needs of modern industries by harnessing the power of interconnected systems, data-driven decision-making, automation, IoT, and other advanced technologies. It offers a transformative approach to manufacturing and production, driving efficiency, agility, and innovation in the face of rapidly changing market dynamics.