ir 4.0 definition
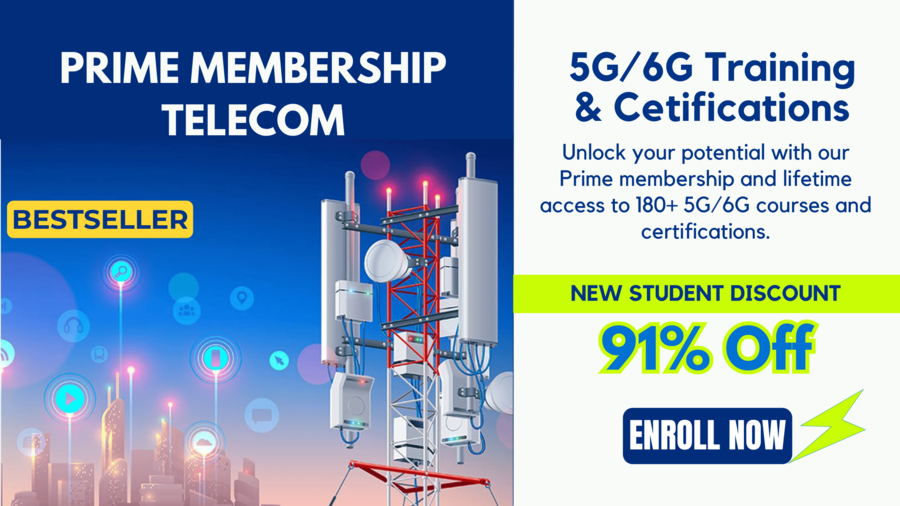
Industry 4.0, often referred to as the Fourth Industrial Revolution or IR 4.0, represents a significant leap in the evolution of industrial processes, combining the cyber-physical systems, the Internet of Things (IoT), and the Internet of Services. This transformation aims to create "smart factories" where machines, systems, and humans communicate and cooperate seamlessly.
Here's a more technical breakdown:
Key Components of Industry 4.0:
- Cyber-Physical Systems (CPS):
- These are systems that integrate computing elements with physical processes. In the context of IR 4.0, CPS refers to machinery and equipment connected via IoT technology that can monitor physical processes and make decentralized decisions.
- Examples include sensors embedded in machines that provide real-time feedback and adjust processes autonomously.
- Internet of Things (IoT):
- IoT represents a network of interconnected devices that communicate and share data with each other over the internet. In the industrial setting of IR 4.0, this involves smart devices and sensors that collect and exchange data.
- Sensors, actuators, and other devices in manufacturing plants can collect data, share it with other systems, and initiate actions based on the received information.
- Big Data and Analytics:
- With the vast amount of data generated by IoT devices and systems, there's a need for advanced analytics tools. Big data analytics processes this data to derive insights, optimize processes, predict maintenance needs, and make informed decisions.
- Machine learning algorithms and AI systems analyze patterns, optimize production processes, forecast demands, and identify anomalies or potential issues.
- Cloud Computing:
- Cloud platforms provide scalable and flexible computing resources essential for handling vast amounts of data, deploying applications, and managing processes in IR 4.0 environments.
- Cloud services enable real-time data processing, storage, and access from anywhere, facilitating collaboration and integration across various systems and locations.
- Augmented Reality (AR) and Virtual Reality (VR):
- AR and VR technologies offer new ways to visualize, design, simulate, and operate industrial processes.
- In manufacturing, AR can provide workers with real-time information, instructions, or guidance overlaying physical objects, while VR can simulate environments for training, design validation, or remote operations.
- Advanced Robotics and Automation:
- Industry 4.0 leverages advanced robotics equipped with sensors, actuators, and AI capabilities to perform complex tasks with precision, flexibility, and efficiency.
- Robots collaborate with humans in tasks such as assembly, packaging, logistics, and quality control, enhancing productivity and safety.
Benefits of Industry 4.0:
- Increased Efficiency and Productivity: Through automation, real-time monitoring, and optimization, IR 4.0 improves production efficiency, reduces waste, and enhances overall productivity.
- Flexibility and Customization: Smart factories enable rapid adjustments to production processes, allowing manufacturers to respond quickly to market demands and produce customized products at scale.
- Predictive Maintenance: IoT sensors and data analytics predict equipment failures or maintenance needs before they occur, reducing downtime and extending equipment lifespan.
- Enhanced Safety: Advanced robotics, AI-driven safety systems, and real-time monitoring contribute to safer working environments, reducing accidents and ensuring compliance with safety standards.