industry 4.0 connectivity
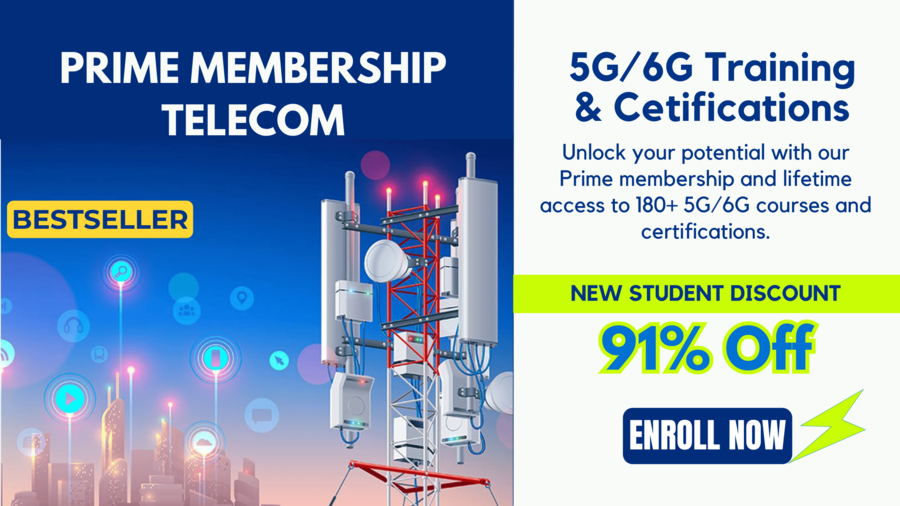
Industry 4.0 refers to the fourth industrial revolution, characterized by the integration of digital technologies into manufacturing and other industrial processes. Connectivity is a key aspect of Industry 4.0, as it involves linking various devices, machines, and systems to enable seamless communication and data exchange. Here's a technical explanation of Industry 4.0 connectivity:
- Internet of Things (IoT): Industry 4.0 relies heavily on the IoT, which involves connecting physical devices and objects to the internet. These devices, often equipped with sensors and actuators, can collect and exchange data. In an industrial setting, this could include sensors on machines, products, or even workers' wearables.
- Cyber-Physical Systems (CPS): CPS integrates computational and physical processes. In Industry 4.0, machines and systems are not only connected to the internet but also equipped with computing capabilities. This enables them to make decentralized decisions based on the data they collect. For example, a production line might adjust its speed based on real-time demand data.
- Cloud Computing: Industry 4.0 leverages cloud computing for storage, processing, and analysis of the massive amounts of data generated by connected devices. Cloud platforms provide the scalability and flexibility needed to handle the diverse data types and volumes in industrial applications.
- Big Data Analytics: The data generated by connected devices in Industry 4.0 is often vast and complex. Big data analytics techniques are employed to derive meaningful insights from this data. This includes predictive maintenance, quality control, and optimization of production processes.
- Edge Computing: In some scenarios, especially where real-time processing is critical, edge computing is used. Edge devices, situated closer to the data source, process and analyze data locally before sending relevant information to the central system. This reduces latency and ensures faster decision-making.
- Communication Protocols: Various communication protocols are used for data exchange between devices and systems. Common protocols include MQTT (Message Queuing Telemetry Transport), CoAP (Constrained Application Protocol), and OPC UA (Open Platform Communications Unified Architecture). These protocols ensure standardized and efficient communication in Industry 4.0 environments.
- Digital Twins: Digital twins are virtual representations of physical objects or systems. In Industry 4.0, machines and processes often have digital twins that mirror their real-world counterparts. These digital twins enable simulation, monitoring, and optimization of physical assets in a virtual environment.
- Security Measures: Given the interconnected nature of Industry 4.0, security is a critical concern. Robust cybersecurity measures, including encryption, authentication, and secure protocols, are implemented to safeguard data and systems from unauthorized access and cyber threats.
- Interoperability: To achieve seamless connectivity, interoperability is essential. Standards and protocols are established to ensure that different devices and systems from different manufacturers can communicate and work together effectively.
By combining these technical elements, Industry 4.0 connectivity aims to create smart, adaptive, and efficient industrial processes that can respond to changing conditions in real-time, improving productivity, and reducing costs.