definition of industry 4.0
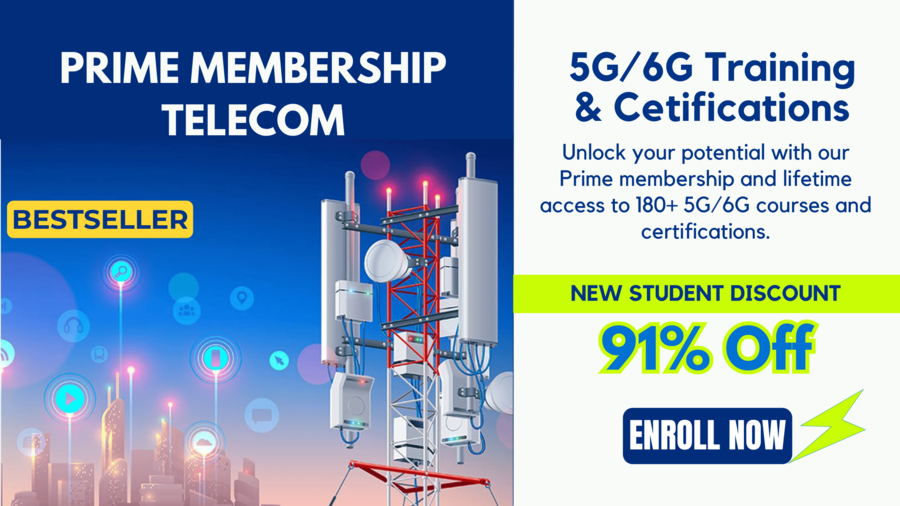
Industry 4.0, also known as the fourth industrial revolution, is a concept that represents the ongoing automation and digitization of traditional manufacturing and industrial practices. It is characterized by the integration of smart technologies, data exchange, and advanced analytics into various aspects of industrial processes. Industry 4.0 aims to create a more connected, efficient, and flexible manufacturing environment. Let's delve into the technical details of this concept:
- Cyber-Physical Systems (CPS): At the core of Industry 4.0 are cyber-physical systems. These are smart systems that integrate computational and physical processes. In manufacturing, this involves embedding sensors, actuators, and communication capabilities into physical objects or processes.
- Internet of Things (IoT): Industry 4.0 relies heavily on the Internet of Things, where devices, machines, and systems are interconnected to share and exchange data in real-time. This connectivity enables seamless communication and collaboration between different components of the manufacturing process.
- Big Data and Analytics: The massive amount of data generated by interconnected devices and sensors is analyzed using advanced analytics. Big data analytics allows manufacturers to derive valuable insights, optimize processes, and make data-driven decisions.
- Cloud Computing: The use of cloud platforms is essential in Industry 4.0. Cloud computing enables the storage and processing of vast amounts of data collected from various sources. It also facilitates access to computing resources and services on-demand.
- Augmented Reality (AR) and Virtual Reality (VR): AR and VR technologies are employed to enhance human-machine interaction and improve training, maintenance, and operation processes. For example, technicians can use augmented reality glasses to access real-time information while performing maintenance tasks.
- Additive Manufacturing (3D Printing): Additive manufacturing technologies play a significant role in Industry 4.0 by allowing for the production of complex and customized components. 3D printing enables rapid prototyping, on-demand production, and the creation of intricate designs that may not be feasible with traditional manufacturing methods.
- Autonomous Systems and Robotics: Industry 4.0 embraces the use of autonomous systems, including robots and drones, for tasks such as material handling, assembly, and inspection. These systems can operate independently or collaborate with human workers.
- Horizontal and Vertical Integration: Horizontal integration involves the connection and communication between different processes and systems within a single manufacturing facility. Vertical integration, on the other hand, involves the integration of processes and systems across the entire supply chain, from suppliers to customers.
- Security and Interoperability: As more devices and systems become interconnected, the importance of cybersecurity and interoperability increases. Industry 4.0 requires robust security measures to protect sensitive data and ensure the seamless flow of information between different components of the system.
Industry 4.0 is a comprehensive transformation of traditional manufacturing through the integration of smart technologies, data-driven decision-making, and enhanced connectivity. It leverages advancements in CPS, IoT, big data analytics, cloud computing, AR, VR, additive manufacturing, autonomous systems, and integration strategies to create more efficient, flexible, and intelligent industrial processes.