DC (Dedicated control)
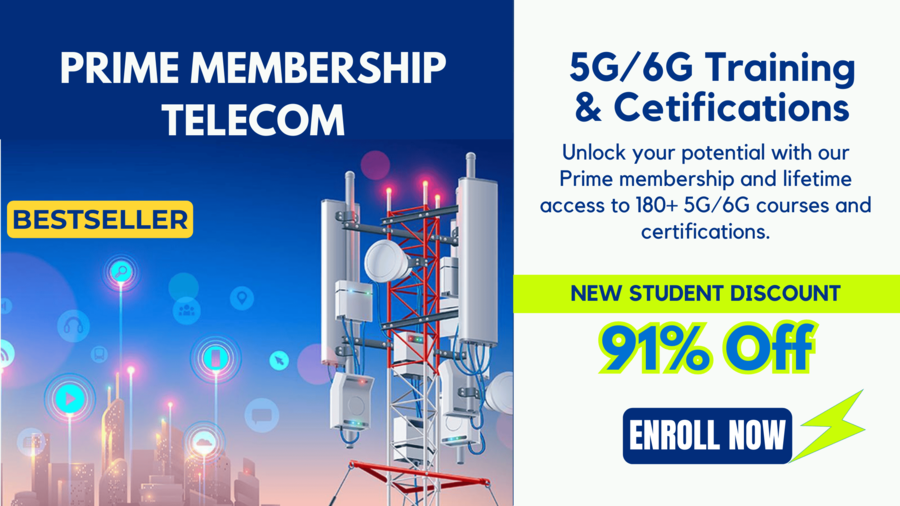
DC (Dedicated Control) is a type of control system that is designed to perform a specific task or set of tasks. It is a control system that is dedicated to a particular function, and it is often used in industrial applications such as manufacturing plants, chemical plants, and power plants. The DC system is a closed-loop system that is designed to regulate a particular variable or process within a plant or system.
DC systems are used to control processes such as temperature, pressure, flow, and level. They consist of a controller, which is the brain of the system, and a set of actuators and sensors that are used to monitor and adjust the process. The controller uses feedback from the sensors to adjust the process to maintain the desired setpoint. The setpoint is the desired value of the variable being controlled.
DC systems can be designed to perform a variety of functions, depending on the specific requirements of the process. For example, a DC system can be designed to regulate the temperature of a chemical reactor, the pressure of a pipeline, or the flow of a liquid through a pipeline. In each case, the DC system would be designed to maintain the desired setpoint within a certain range of values.
The basic components of a DC system are:
- Controller - The controller is the brain of the DC system. It receives feedback from the sensors and uses that information to adjust the process to maintain the desired setpoint. The controller can be a simple device such as a thermostat or a more complex device such as a PLC (Programmable Logic Controller).
- Actuators - Actuators are devices that are used to adjust the process. They can be electric, pneumatic, or hydraulic devices, depending on the specific requirements of the process. The actuators are controlled by the controller and are used to adjust the process to maintain the desired setpoint.
- Sensors - Sensors are devices that are used to monitor the process. They can be temperature sensors, pressure sensors, flow sensors, or level sensors, depending on the specific requirements of the process. The sensors send feedback to the controller, which uses that information to adjust the process to maintain the desired setpoint.
The advantages of DC systems are:
- Efficiency - DC systems are designed to perform a specific task or set of tasks, which makes them more efficient than general-purpose control systems. They are optimized for the specific process that they are controlling, which means that they can operate more efficiently and with greater precision.
- Reliability - DC systems are typically more reliable than general-purpose control systems. They are designed to perform a specific function, which means that they are less likely to fail or malfunction.
- Safety - DC systems can be designed to operate safely in hazardous environments. For example, they can be designed to operate in areas with high temperatures, pressures, or levels of toxicity.
- Flexibility - DC systems can be customized to meet the specific requirements of a process. They can be designed to operate with different types of sensors and actuators, depending on the specific requirements of the process.
The disadvantages of DC systems are:
- Cost - DC systems can be expensive to design and implement. They require specialized knowledge and expertise to design and implement, which can drive up the cost of the system.
- Limited functionality - DC systems are designed to perform a specific task or set of tasks, which means that they have limited functionality. They are not designed to perform multiple functions, which means that they may not be suitable for complex processes.
- Maintenance - DC systems require regular maintenance to ensure that they are operating properly. They may require specialized maintenance and repair services, which can be costly.
In conclusion, DC (Dedicated Control) is a type of control system that is designed to perform a specific task or set of tasks. DC systems are typically used in industrial applications such as manufacturing plants, chemical plants, and power plants, where precise control of processes such as temperature, pressure, flow, and level is essential for efficient and safe operation.
DC systems are designed to be closed-loop systems, which means that they use feedback from sensors to adjust the process and maintain the desired setpoint. The controller is the brain of the system, and it uses feedback from the sensors to adjust the actuators and maintain the desired setpoint.