case study on industry 4.0
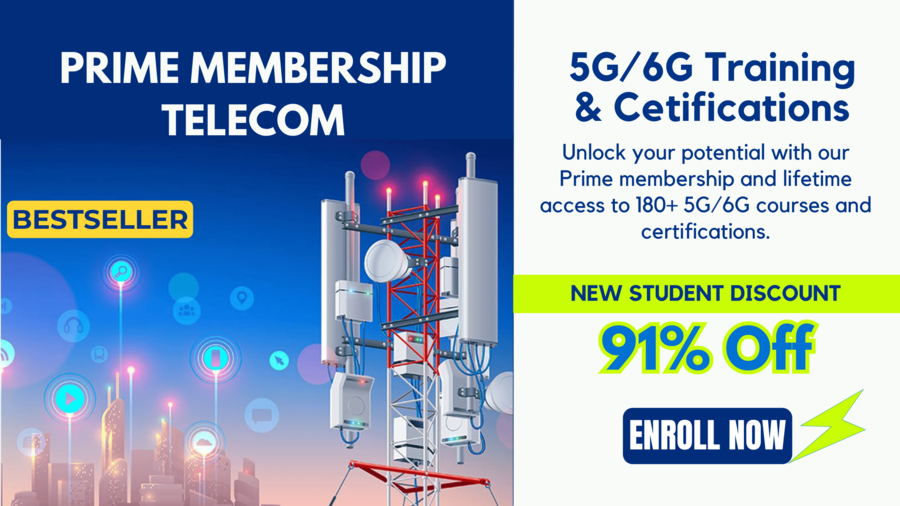
Let's delve into a detailed technical case study on Industry 4.0.
Case Study: Implementation of Industry 4.0 in a Modern Manufacturing Facility
Background:
Company XYZ is a leading manufacturer of automotive components with multiple production facilities globally. To maintain its competitive edge and address evolving market demands, XYZ decided to implement Industry 4.0 principles in its flagship manufacturing plant located in Country A.
Objectives:
- Enhance operational efficiency by leveraging advanced technologies.
- Reduce production downtime through predictive maintenance.
- Improve supply chain visibility and responsiveness.
- Facilitate real-time data-driven decision-making.
Technologies and Solutions Implemented:
- IoT (Internet of Things):
- Sensor Deployment: Installed a network of sensors across machinery and equipment to monitor parameters such as temperature, pressure, vibration, and energy consumption in real-time.
- Data Transmission: Integrated sensors with a centralized IoT platform to transmit data securely and efficiently.
- Big Data and Analytics:
- Data Collection: Collected vast amounts of data from sensors, machinery, and other production systems.
- Data Processing: Utilized cloud-based platforms and edge computing to process and analyze data in real-time.
- Predictive Analytics: Implemented machine learning algorithms to forecast equipment failures, optimize maintenance schedules, and improve overall equipment efficiency (OEE).
- Cyber-Physical Systems (CPS):
- Automated Systems: Integrated automated guided vehicles (AGVs), robotic arms, and conveyor systems to create a seamless production flow.
- Real-time Monitoring: Enabled real-time monitoring and control of CPS using a centralized control system, ensuring synchronization and efficiency.
- Augmented Reality (AR) and Virtual Reality (VR):
- Training and Simulation: Utilized AR/VR technologies for training operators, simulating production scenarios, and optimizing workflows.
- Remote Assistance: Implemented AR solutions to provide remote technical support, reducing response times and minimizing downtime.
- Blockchain Technology:
- Supply Chain Transparency: Implemented blockchain to enhance supply chain visibility, traceability, and authenticity across the entire value chain.
- Smart Contracts: Utilized smart contracts for automated verification, validation, and execution of transactions, contracts, and agreements.
Outcomes and Benefits:
- Operational Efficiency: Achieved a significant improvement in production efficiency, reducing cycle times and enhancing throughput.
- Predictive Maintenance: Reduced unplanned downtime by over 30% through predictive maintenance, minimizing equipment failures and associated costs.
- Supply Chain Optimization: Enhanced supply chain visibility, responsiveness, and agility, resulting in improved inventory management and reduced lead times.
- Data-Driven Decision Making: Empowered decision-makers with real-time data and insights, facilitating proactive decision-making and strategic planning.
- Cost Savings: Realized substantial cost savings through optimized resource utilization, reduced wastage, and enhanced productivity.
Challenges and Lessons Learned:
- Data Security and Privacy: Ensured robust cybersecurity measures to protect sensitive data and maintain data privacy.
- Skill Gap: Addressed the skill gap by providing training and development programs to upskill employees and foster a culture of continuous learning.
- Integration Complexity: Managed the complexity of integrating diverse technologies and systems by adopting a phased approach, ensuring seamless integration and interoperability.
Conclusion:
By embracing Industry 4.0 principles and leveraging advanced technologies, Company XYZ transformed its flagship manufacturing plant into a state-of-the-art facility, achieving significant improvements in operational efficiency, predictive maintenance, supply chain optimization, and data-driven decision-making. The successful implementation serves as a blueprint for future expansion and digital transformation initiatives across the organization, reinforcing its position as a leader in the automotive components industry.