application of industry 4.0 in manufacturing
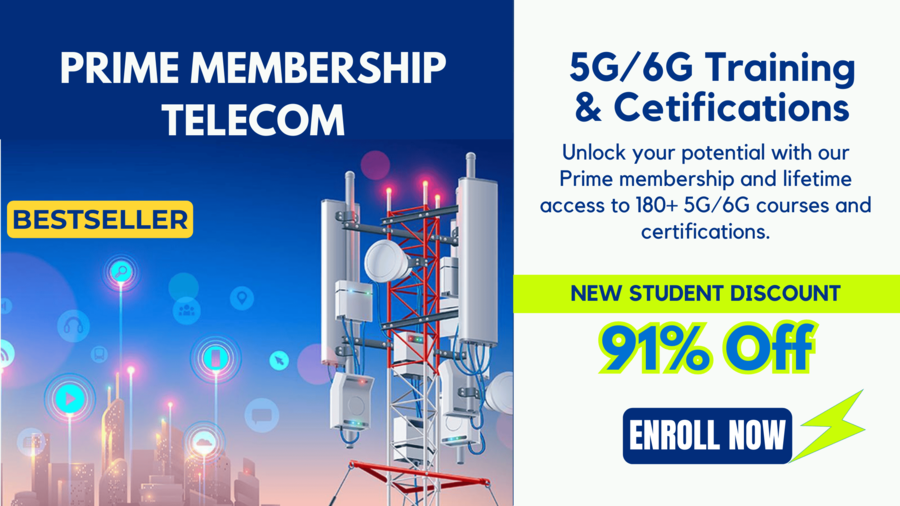
Industry 4.0, also known as the Fourth Industrial Revolution, represents a paradigm shift in manufacturing that integrates advanced digital technologies, data analytics, and the Internet of Things (IoT) to create "smart factories." These smart factories are characterized by the seamless integration of physical and digital systems, resulting in more efficient, flexible, and intelligent manufacturing processes. Let's explore the technical details of the application of Industry 4.0 in manufacturing:
1. IoT and Connectivity:
- Sensors and Actuators:
- Integration of a multitude of sensors and actuators on machines, equipment, and even products themselves. These devices collect real-time data on parameters such as temperature, pressure, vibration, and machine status.
- Connectivity Protocols:
- Implementation of communication protocols like MQTT, CoAP, or OPC UA to facilitate seamless data exchange between devices and systems.
- Edge Computing:
- Utilization of edge computing to process data at or near the source, reducing latency and enabling faster decision-making.
2. Data Analytics and Big Data:
- Data Collection and Storage:
- Collection and storage of massive amounts of data from various sources, including sensors, machines, and production processes.
- Big Data Analytics:
- Application of big data analytics tools and techniques to derive meaningful insights from the collected data. This includes predictive maintenance, quality optimization, and production planning.
- Machine Learning Algorithms:
- Implementation of machine learning algorithms for predictive analysis and anomaly detection, allowing manufacturers to anticipate and prevent equipment failures.
3. Digital Twin Technology:
- Virtual Replication:
- Creation of digital twins, virtual replicas of physical assets or processes, using data from sensors and other sources. This enables real-time monitoring and analysis of physical systems.
- Simulation and Optimization:
- Use of digital twins for simulation and optimization of manufacturing processes, allowing manufacturers to test different scenarios and identify the most efficient production strategies.
- Remote Monitoring and Control:
- Digital twins facilitate remote monitoring and control of physical assets, enabling operators to make adjustments and optimize processes from a centralized location.
4. Automation and Robotics:
- Collaborative Robots (Cobots):
- Integration of collaborative robots that can work alongside human operators, enhancing efficiency and safety on the factory floor.
- Automated Guided Vehicles (AGVs):
- Implementation of AGVs for material handling and logistics, guided by sensors and controlled through centralized systems.
- Automated Production Lines:
- Automation of production lines with smart machines and robotic arms that can adapt to different product specifications and configurations.
5. Cyber-Physical Systems (CPS):
- Interconnected Systems:
- Integration of cyber-physical systems where physical machines, devices, and processes are connected through a network to enable real-time communication and collaboration.
- Real-Time Decision-Making:
- Cyber-physical systems enable real-time decision-making by leveraging data from the physical environment and adjusting operations accordingly.
- Decentralized Control:
- Implementation of decentralized control systems that distribute decision-making processes across various components, reducing reliance on a centralized control structure.
6. Additive Manufacturing (3D Printing):
- Prototyping and Production:
- Use of 3D printing for rapid prototyping and on-demand production, allowing manufacturers to quickly iterate designs and customize products.
- Complex Geometries:
- 3D printing enables the production of complex geometries that would be challenging or impossible to achieve with traditional manufacturing methods.
- Reduced Waste:
- Additive manufacturing reduces material waste by only using the necessary amount of material for production, contributing to sustainability.
7. Augmented Reality (AR) and Virtual Reality (VR):
- Training and Maintenance:
- Use of AR and VR for employee training and maintenance tasks, providing step-by-step instructions and visual aids.
- Assembly and Quality Control:
- AR can assist workers in assembly tasks by overlaying digital information on physical components, while VR can be used for immersive quality control inspections.
- Remote Assistance:
- AR facilitates remote assistance, allowing experts to guide on-site personnel through complex tasks using real-time visualizations.
8. Supply Chain and Logistics Optimization:
- Predictive Supply Chain Management:
- Implementation of predictive analytics to optimize supply chain management, including demand forecasting, inventory management, and logistics planning.
- Blockchain for Traceability:
- Integration of blockchain technology for enhanced traceability and transparency in the supply chain, reducing the risk of counterfeiting and ensuring the authenticity of products.
- Smart Warehousing:
- Use of IoT sensors and automation in warehouses for real-time inventory tracking, reducing errors and improving overall efficiency.
9. Human-Machine Interaction (HMI):
- Intuitive Interfaces:
- Implementation of intuitive and user-friendly interfaces for operators to interact with machines and systems, enhancing usability and reducing training times.
- Wearable Devices:
- Use of wearable devices equipped with sensors to monitor the health and safety of workers, providing real-time feedback and alerts.
- Voice and Gesture Control:
- Integration of voice and gesture control interfaces to enable hands-free operation in environments where manual input may be challenging.
10. Security and Cybersecurity Measures:
- Secure Communication Protocols:
- Implementation of secure communication protocols, encryption, and authentication mechanisms to protect data integrity and privacy.
- Network Segmentation:
- Network segmentation to isolate critical systems and prevent unauthorized access to sensitive data and control systems.
- Continuous Monitoring:
- Continuous monitoring of the manufacturing environment for anomalies and potential security threats, with the implementation of intrusion detection systems.
11. Environmental Sustainability:
- Energy Monitoring and Management:
- Integration of energy monitoring systems to optimize energy consumption and reduce environmental impact.
- Waste Reduction:
- Implementation of smart processes to minimize waste generation and enhance the recyclability of materials.
- Green Manufacturing Practices:
- Adoption of eco-friendly manufacturing practices supported by real-time data analytics for resource optimization.
12. Interoperability and Standardization:
- Open Standards:
- Adoption of open standards, such as OPC UA (Unified Architecture), to ensure interoperability between different devices and systems from various manufacturers.
- Integration Platforms:
- Use of integration platforms and middleware to connect heterogeneous systems, allowing seamless communication and data exchange.
- Data Standardization:
- Standardization of data formats and structures to enable consistent and meaningful information exchange across the manufacturing ecosystem.
13. Cloud Computing:
- Scalability and Flexibility:
- Utilization of cloud computing for scalable storage, processing power, and data analytics, providing manufacturers with flexibility in resource allocation.
- Remote Access and Collaboration:
- Cloud-based solutions enable remote access to manufacturing data and support collaborative efforts between geographically dispersed teams.
- Disaster Recovery:
- Implementation of cloud-based disaster recovery solutions to ensure data resilience and business continuity.
14. Regulatory Compliance and Quality Assurance:
- Traceability Systems:
- Implementation of traceability systems to comply with regulatory requirements and ensure the ability to trace the origin and production history of products.
- Quality Control Systems:
- Integration of advanced quality control systems using sensors and vision systems to ensure product quality and adherence to industry standards.
- Audit Trails and Documentation:
- Automated generation of audit trails and documentation to facilitate compliance with regulatory standards and certifications.
15. Maintenance and Predictive Analytics:
- Predictive Maintenance:
- Implementation of predictive maintenance systems that use data from sensors and analytics to anticipate equipment failures and schedule maintenance activities proactively.
- Condition Monitoring:
- Continuous condition monitoring of machinery to detect subtle changes or anomalies in performance that may indicate impending issues.
- Prescriptive Analytics:
- Use of prescriptive analytics to recommend optimal maintenance strategies based on historical data and real-time conditions.
16. Challenges and Considerations:
- Security Concerns:
- Addressing cybersecurity challenges to protect against data breaches, unauthorized access, and potential disruptions to manufacturing processes.
- Skill Gaps:
- Bridging the skills gap by providing training and education for the workforce to adapt to new technologies and processes introduced by Industry 4.0.
- Interoperability Challenges:
- Ensuring seamless integration and interoperability between diverse systems and technologies from different vendors.
- Data Privacy:
- Addressing concerns related to data privacy and ensuring compliance with regulations, especially when dealing with sensitive information.
- Initial Investment:
- Overcoming the initial investment required for the implementation of Industry 4.0 technologies, considering the long-term benefits and return on investment.
In summary, the application of Industry 4.0 in manufacturing involves the integration of advanced technologies, data analytics, and connectivity to create intelligent and efficient production systems. The technical aspects cover a broad spectrum, from IoT and connectivity to automation, analytics, and advanced human-machine interaction. Successful implementation requires addressing challenges and considering factors such as security, interoperability, and workforce readiness.