4.0 industrial
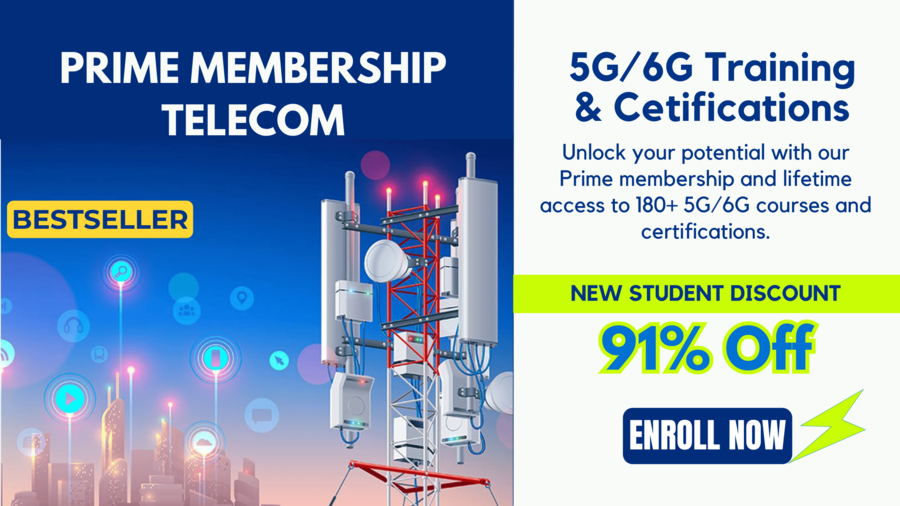
The term "Industry 4.0" refers to the fourth industrial revolution, characterized by the integration of digital technologies into various aspects of industrial processes. It builds upon the previous three industrial revolutions, each marked by significant advancements in manufacturing and production:
- First Industrial Revolution (late 18th to early 19th centuries): Mechanization of production using water and steam power.
- Second Industrial Revolution (late 19th to early 20th centuries): Introduction of electricity and assembly line production.
- Third Industrial Revolution (mid-20th century): Adoption of computers and automation in manufacturing.
Now, let's delve into the technical aspects of Industry 4.0:
Key Technological Components of Industry 4.0:
- Internet of Things (IoT): Devices and machines are equipped with sensors and actuators to collect and exchange data in real-time. This connectivity enables seamless communication between different components in the manufacturing process.
- Big Data and Analytics: The massive amount of data generated by IoT devices is processed and analyzed to derive valuable insights. This includes predictive maintenance, quality control, and optimization of production processes.
- Cloud Computing: Centralized storage and processing of data in the cloud facilitate accessibility and collaboration. It also supports the scalability required for handling large datasets.
- Cyber-Physical Systems (CPS): The integration of physical processes with digital systems allows for real-time monitoring, control, and optimization. CPS forms the backbone of smart factories.
- Augmented Reality (AR) and Virtual Reality (VR): These technologies are employed for training, maintenance, and simulation purposes. AR, for instance, can overlay digital information onto the physical environment, aiding workers in tasks.
- Additive Manufacturing (3D Printing): This technology enables the production of complex, customized, and on-demand products. It reduces waste and allows for more efficient use of materials.
- Autonomous Robots: Robots equipped with AI and machine learning capabilities can perform tasks independently, such as material handling, assembly, and quality control.
- Horizontal and Vertical Integration: Horizontal integration involves connecting different processes within the manufacturing environment, while vertical integration links the entire supply chain, from suppliers to customers.
- Digital Twin: A digital representation of a physical object or system. It allows for simulation and analysis of the real-world counterpart, aiding in design, monitoring, and maintenance.
Benefits of Industry 4.0:
- Increased Efficiency: Real-time data and analytics optimize production processes, reducing downtime and improving overall efficiency.
- Flexibility and Customization: The ability to quickly adapt production processes allows for greater customization and responsiveness to market demands.
- Cost Reduction: Predictive maintenance, efficient resource utilization, and reduced waste contribute to cost savings.
- Improved Quality: Continuous monitoring and analysis of data enable better quality control and defect prevention.
- Enhanced Safety: Autonomous robots and AI-driven systems can handle dangerous tasks, improving workplace safety.
Challenges and Considerations:
- Security Concerns: The increased connectivity also brings about heightened cybersecurity risks. Protecting sensitive data and systems is crucial.
- Workforce Skills: Industry 4.0 requires a skilled workforce capable of working with advanced technologies. Training and education are essential.
- Interoperability: Ensuring that different devices and systems can communicate seamlessly is a significant challenge. Standardization efforts are ongoing.
- Ethical Implications: As automation increases, ethical considerations related to job displacement, privacy, and data usage come to the forefront.
Industry 4.0 represents a paradigm shift in manufacturing, leveraging digital technologies to create smarter, more efficient, and interconnected industrial systems. The integration of IoT, data analytics, AI, and other technologies enhances productivity, quality, and innovation in manufacturing processes.